FREE
Facilitator: Evan Hyde – REFCOMM®
Overview
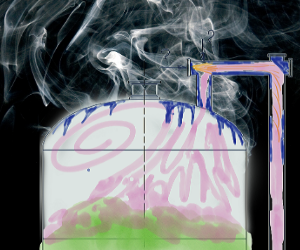
Our goal is to keep the coke in the coke drum, right? We are not always completely successful in this mission but one way to keep the drum vapor line clean is to minimize carryover from the drum and quench the vapors “enough” to prevent coke deposition on the ID of the pipe. Coke deposits in the line increase drum pressure and negatively impact yields. Conversely, quenching too much can create excess recycling that limits capacity. In this session, we will explore this tight rope and discuss what a good quenched vapor target could be for your plant.
Webinar Recap
Another successful eRefComm® event!!!! We want to thank the more than 250 people who registered and participated in the event. The diversity of experiences with this challenging piping circuit was impressive. Of all the 100’s of miles or kilometers of piping in a delayed coker, the fact that this small piece of pipe, around 100ft (30m) long, can give us such headaches and opportunities for profitability improvement is important to keep in mind.
By in large, most of the fouling occurs in the donut section of the coke drum nozzle, just before the first turn at the drum outlet vapor line. Velocities in a normal coke drum are around 0.7ft/s (0.21 m/s) but the drum vapor line is very fast at 130+ ft/s (41m/s) so the residence time in the drum vapor line is very small. This picture, looking down into the coke drum from above, shows an example of the donut.
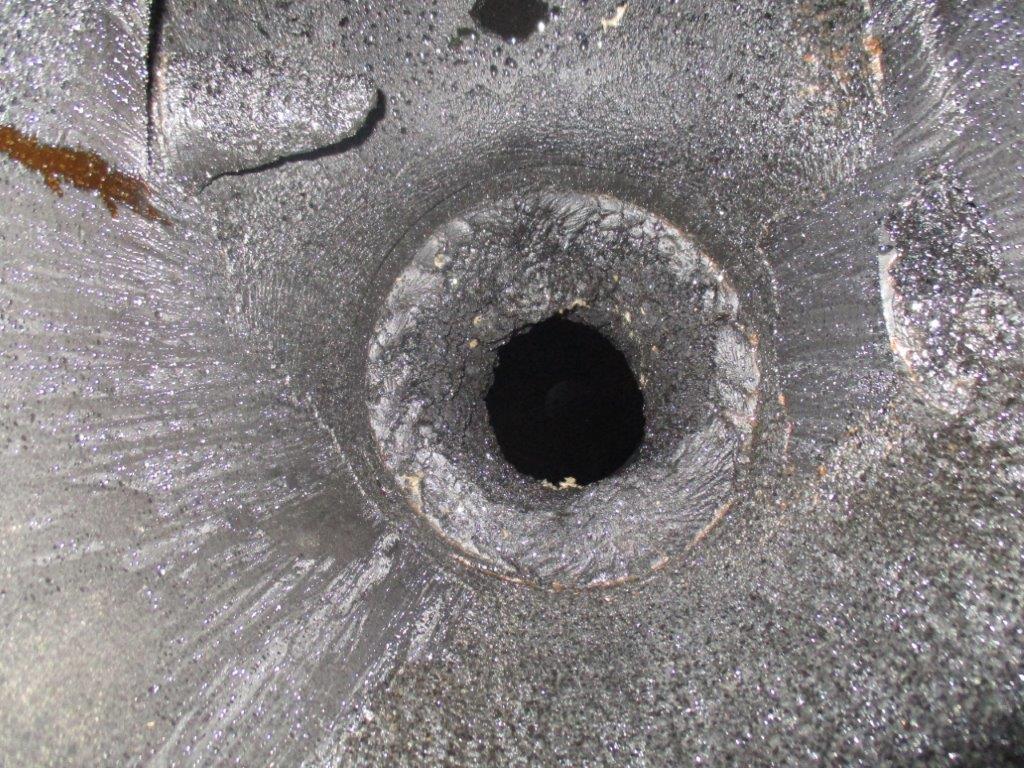
If the coke accumulation gets severe enough, the increased pressure drop in the line will increase drum pressure, which negatively impact yields. Therefore, it is a good idea to periodically clean the drum nozzle (donut coke) to regain the lower pressure drop and lost yield. This type of cleaning can be accomplished online after cutting is complete. It is important to keep the vapor line clear downstream of the quench injection location because that section of line can only be effectively cleaned during a turnaround or extended pigging outage.
In the first survey, we learned that the vast majority of sites are quenching their drum overhead vapors to around 800-780°F (426-415°C). This makes sense because the magic temperature for the rate of reaction increase for thermal cracking is around 800°F so getting below this temperature is a good idea. It was interesting to note that others were quenching far more than this temperature threshold. What are they seeing that is trending them in this direction? It is possible they have other issues to contend with like pressure drop, HCGO quality issues, or high recycle in the base case and therefore, have little concern about the natural recycle from the drum vapors. It is hard to see all the reasons from this simple survey, but the consensus is clear.
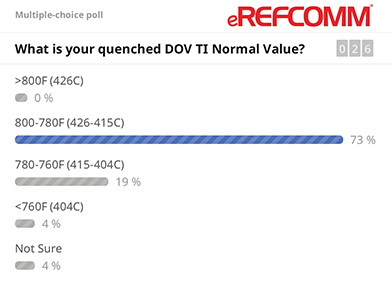
There are a variety of quenching strategies/control strategies but most of the poll respondents control to an absolute temperature. It was interesting that many respondents to the next poll were only using the licensor values, which were provided who knows how long ago, to optimize the unit. The runner-up response was setting the control point to reduce fouling over time, which makes more sense from a long-term optimization strategy. The licensor value is a good starting point but should be improved over time.
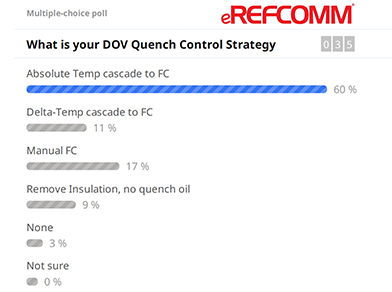
The next part of the discussion was focused on the various types of designs, but the major common element is the liquid. The liquid is meant to wet the walls of the drum vapor line and keep any entrained or created coke moving down the pipe to the fractionator where it can be removed through the fines removal system. Lastly, there was an interesting discussion around what are the optimum sources of quench oil. Over the years, sites have used a variety of different materials from LCGO, HCGO, slop oil (internal and external), and other creative streams…..that’s where the magic is and some big economic benefits if you properly select a stream here. If you want to know more about those streams and how it might work at your site, please contact us at info@coking.com so we can perform an engineering evaluation of what might work for your site.
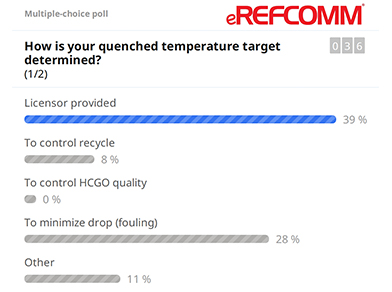