Refinery operators know that proper process variable measurements are critical to the safe and efficient operation of every refinery process unit. Field instrument data becomes compromised when instrument taps have become partially blocked or are plugged from dirty, scaling, and sooty processes. That reduces operating efficiency, costs a refinery thousands of dollars, and most importantly, increases the risk of bodily harm to refinery workers.
We will first address some frequently used methods to treat the problem of plugged taps that we DON’T recommend and we’ll explain why. They include the use of oversized taps, excessive purge use, manual rodding and blowing down, operating blind, and using the alert function in advanced diagnostic pressure.
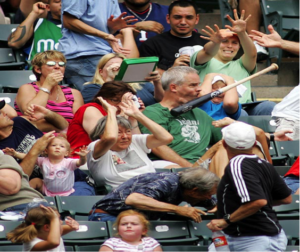
Don’t get smacked by plugged tap lines!
- Let’s start with the most important one– manual clearing techniques. Risking life and limb to manually unblock a recurrent blockage is expensive and dangerous. It exposes refinery workers to unnecessary risk and requires the process loop to be isolated and out of production.
- Continuous high flowing purge system. This technique is not ideal because of the excessive parasitic purge use that is required.
- Portable pumper hand-cart. Again, not advisable because the operator has to be nearby to clear the path.
- Special block valves with rod through capability. This also poses a safety risk to the operator.
- SMART field transmitters. These are great for alerting operators that a tap bore is partially plugged, but manual remedial action or unit outages are still required to clear the tap.
The Solution
Instead of exposing teams to danger or implementing half-measures, it is far more effective to use an
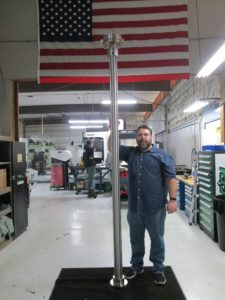
Clearguard Autorodder
Autorodder. By stroking a custom built scraper through the tapping point at a predetermined frequency (anywhere from once per hour to once per day or week) the Autorodder provides the following benefits:
- The pressure transmitter and differential pressure transmitter can be used in dirty, crystallizing applications reliably and confidently. No need for expensive field instruments.
- Purge flow can be reduced to an absolute minimum so that it can do its job and that is act as a barrier.
- Technicians are never exposed to the risky practice of manually rodding out plugged tapping points.
- Accurate and reliable process variable measurement = accurate process control = maximum unit efficiency.
- By maintaining a clear tapping point and eliminating any possible purge backflow, plugged impulse lines are no longer a problem.
- Spurious outages or unit shutdowns from plugged tapping points become obsolete.
- The autorodder apparatus can be locally operated and controlled or connected to your DCS.
- The autorodder requires no special tools, is field serviceable and interchangeable.
Case Studies
Let’s Examine Two Case Studies Provided by Clearguard, an automatic rodding solutions company that focuses on safe and reliable Pv (pressure, level and flow) measurement systems:
Application #1 | 392°F acid, pressure / level measurement tapping point |
Manual rodding frequency | Once per day |
Autorodder | 1-1/4” diameter cylinder, 25-1/2” stroke with a 1” ANSI 150# process connection |
Control solution | Class 1, Div. 2 |
Stroke frequency | Once every 2 hours |
Result | Saving 4,000USD per month per Autorodder |
ROI | 2 months (incl. cost of installation) |
Application #2 | 1200°F reactor feed nozzle |
Manual rodding frequency | 16+ times per year |
Autorodder | 3-1/4” diameter cylinder, 98-1/2” stroke with 4” ANSI 150# process connection. All wetted parts are Inconel 600 |
Control solution | Customer provided |
Stroke Frequency | Once per day |
Result | Saving 1,200,000 per year |
ROI | 1 month |
If you want to learn more about autorodding solutions, stop by Clearguard’s booth at RefComm® 2018 Galveston.
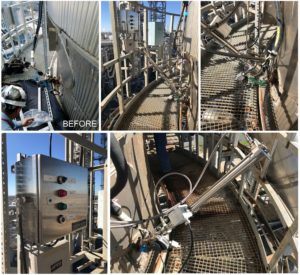
Autorodders prevents plugged taps
Clearguard Vice President Ben Cammack plans to introduce the Clearguard autorodder to customers that are not currently aware of the technology and he will also have multiple working demonstration autorodders on display. For more information, contact Ben at ben.c@clearguard.com
Leave a Reply
You must be logged in to post a comment.