How long is your plant willing to wait to clean (a.k.a. decoke, line mole, hydroblast, or– my personal favorite– “Clean the Donut”) the drum vapor line?
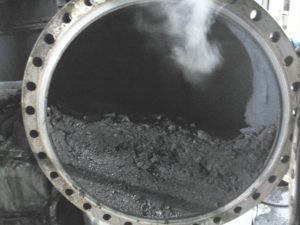
DOV Opening for Cleanout 6
Determining the optimum frequency is site specific but when we look at some select factors, we often arrive at the same conclusion: you should be cleaning it more often than you are. This will pay significant dividends in the form of yield improvement.
New Delayed Cokers– like those by Bechtel, Amec Foster Wheeler or Lummus– are designed with a minimal pressure drop between the coke drum and the fractionator flash zone to increase liquid yields. In many cases, it is not uncommon to see vapor lines +24″. The typical design pressure drop is 2-5 psig only. However, in site performance assessments, it is common to see the dP exceeding 4-5 psig above the clean state.
This is costing real money!
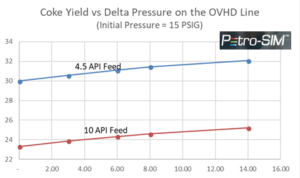
Pressure vs Yield PetroSIM
Yes, finding the yield shift in the poor DCU material balance will be hard, but there is enough science to demonstrate it is real to keep the economics on solid ground. Based on the PetroSIM DCU model, each PSI is worth (-0.16 wt%) reduction in coke yield. These products will be distributed in the yields but most of the incremental molecules will be HCGO. Assuming your HCGO goes to either an FCC or HDC, the marginal value of the extra HCGO will be $5-20+/BBL. Assuming a margin of $10/bbl on a 50kbd coker, the value of cleaning the vapor line at 2 psig versus 5 psig over the clean state is: 3 psig > 240 bpd+ HCGO > 876k$/year!
I could be wrong, but I think you can pay the salaries for a lot of maintenance guys to do this cleaning more regularly with those profit margins. At one recent plant visit, I observed operators doing the donut cleaning without maintenance support. That was amazing! Just make sure you torque the bolts on the dollar plate properly, guys….
Here are some cleaning frequency recommendations with proven success:
- Clean the donut when the dP exceeds +1.5-2.0 psig over the clean condition (i.e. design = 1.5, clean at 3.0, or design = 5 psig clean, then clean at 7 psig).
- Clean the entire vapor line to the fractionator during every major turnaround.
- Optimize the drum vapor quench flow rate and nozzle design to reduce accumulation. Do a flash simulation to ensure the walls of the vapor line are liquid wet all the way to the fractionator. If dP gets too high, dry points can be created which accelerate coke accumulation.
Check out the recent presentation given at RefComm® Galveston 2018 by Sim Romero and Maria Aldescu about PetroSIM model results and new correlations.
For more information, feel free to contact me directly or visit www.RefiningCommunity.com.
Leave a Reply
You must be logged in to post a comment.