THE ISSUES
- Drum Bulging & Cracking. One of the most common failure mechanisms of a coke drum shell is the bulging and cracking of the cylindrical pressure boundary. These failures are typically aligned with the circumferential welds, with similar failures appearing in vertical plate “seamless” vessels designs as well. In addition to bulging and cracking, localized crack repair and emergent bridge repairs have become more commonplace.
- Skirt Cracking Repairs. Other common failure mechanisms are associated with support skirts and their associated attachment welds, such as skirt repair geometries, skirt attachment zone base metal repair, and sectional skirt partial replacement. Coker vessel skirt attachment geometries vary by designer and age of the vessel with the attachment point a common source of failure, making the design and implementation of the repair complex.
Coker Skirt Cracking
- Other Coke Drum Mechanism Issues. Less common issues in vessel operation include corrosion under insulation (CUI), blow down piping fatigue failures, and cone replacement welding.
SOLUTIONS OFFERED BY AZZ
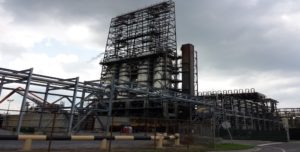
Coker Unit
- Drum Bulging & Cracking. AZZ, the largest global provider of structural repairs for coking units, has effectively addressed the bulging and cracking issue with a temperbead structural overlay process. This unique process of installing a highly engineered weld metal overlay to the existing vessel to modify the structure of the vessel mitigates bulging and cracking caused by the low cycle fatigue mechanisms to which the vessels are exposed. Because the welding parameters are tightly controlled by the use of closed loop automated welding systems, controlled deposition techniques (temperbead) are implemented to eliminate the need to perform post weld heat treatment of the structural overlay deposit. In cases where owners choose localized crack repair, deferring implementation of a structural overlay for a later time, AZZ has performed these repairs to obtain proper tempering of the repair area without the need for post weld heat treatment. The company has also provided external structural overlay solutions as well as analysis support to help bridge the gap for clients between the next maintenance turnaround.
- Skirt Cracking Repairs. For support skirt crack repairs, AZZ Specialty Welding utilizes a proprietary welding processes to replace the critical skirt attachment welds and in some cases install new sections of skirt also without requirement for post weld heat treatment. This approach has been demonstrated to be superior to conventional methods of repair. Utilizing a machine controlled temperbead welding process to minimize the likelihood of volumetric defects and provide a tempered heat affected zone, AZZ offers a variety of skirt repairs that address the most common failure modes and configurations. AZZ’s machine-controlled welding techniques effectively address skirt attachment failures as well as cracking in the vessel where the skirt would attach. In some cases, AZZ can address this issue by replacing the entire attachment zone of the vessel and replace it with new material. In cases where a complete replacement of a section of the skirt is required, AZZ provides a complete service including design activities necessary to determine the maximum section size and quantity of sections that can be replaced in parallel with acceptable vessel stability. AZZ offers several proprietary approaches to resolve issues with the attachment weld geometry as well as maximize the life of the skirt.
- Other Coke Drum Mechanism Issues. While older coker units with inadequate insulation designs can experience significant corrosion under insulation, AZZ has the experience and engineered solutions to restore vessel pressure boundary in almost any location by weld metal buildup. AZZ reinforces the circumferential seam welds in blow down piping with a structural weld overlay to address a common thermal fatigue cracking issue found in these locations. AZZ’s patented HotPulse™ TIG welding process has proven ideal for the performance of these critical welds and the best approach for welding extremely high stress area such as on a cone replacement. The volumetric quality and mechanical properties attained the HotPulse TIG process are significantly better than conventional welding techniques.
ABOUT AZZ
AZZ Specialty Welding’s (formerly WSI) commitment to innovative life extension repairs for delayed coker unit components dates back more than 30 years with the first structural overlay mitigation of shell bulging project performed in 1986. For more than 30 years, AZZ’s Specialty Welding Division has developed a complete portfolio of life extension solutions, procedures and processes to successfully address a wide range of challenges faced by coker unit managers.
As the global leader in life extension repairs for delayed coker units, AZZ Specialty Welding partners with research and educational institutions (e.g., National Science Foundation, Ohio State University Manufacturing & Materials Joining Innovation Center, NSF Cooperative Research Center) in driving advances in life extension solutions, procedures and processes that successfully address a wide range of challenges created by coker unit operation.
AZZ at REFCOMM®
AZZ will be exhibiting at RefComm® Galveston 2018, where they hope to gain additional insight into the trends, challenges and demands of the energy industry. They also hope for the opportunity to engage and interact with past customers, potential future customers, fellow travelers and partners in the refining community. AZZ will most likely be demonstrating the company’s proprietary processes that have been successfully implemented for coke unit life extension. Click here to register for RefComm® so you can check out what AZZ has to offer, along with dozens of other innovative companies. Once registered, you can download the RefComm® app to schedule an appointment with AZZ Senior Project Manager Pete Sanders. For more information, visit AZZ’s website.
Leave a Reply
You must be logged in to post a comment.