Let’s say you have a sink and the faucet handle breaks or rounds off. Then you put pipe wrench on the stub where the faucet handle was to get water in the sink. Sure, you’ve found a workaround to get the water flowing, but you’ve also just changed the way the sink was originally designed to function.
The same concept applies in the refinery. There are certain protocols put into place by engineering, PSM, and equipment manufacturers is designed to be operated in a certain way. You’re not supposed to deviate from the normal way of operating the equipment– from the way it was originally designed– just to make it fit your need today without letting management, engineering and supervision know that you changed the way the equipment functioned for operational needs.
Sure, you can change the basic functioning of the sink as it was designed, if you absolutely need to. But then there needs to be a Management of Change (MOC): the proper paperwork needs to be completed, and protocols executed, to ensure the safety of those who use the sink faucet after you.
According to the Washington State Department of Labor & Industries, “Management of Change, or MOC, is a best practice used to ensure that safety, health and environmental risks are controlled when a company makes changes in their facilities, documentation, personnel, or operations.”
By their very nature, MOC programs are designed to ensure that all changes to a process are properly reviewed, and “any hazards introduced by the change are identified, analyzed, and controlled before resuming operation.”
Here’s an excerpt from the U.S. Chemical Safety & Hazard Investigation Board about Management of Change (MOC):
Chemical processing enterprises should establish policies to manage deviations from normal operations. Systematic methods for managing change are sometimes applied to physical alterations, such as those that occur when an interlock is bypassed, new equipment is added, or a replacement is “not in kind.” The operating plant needs to have MOC policies that include abnormal situations, changes to procedures, and deviations from standard operating conditions.
For an MOC system to function effectively, field personnel need to know how to recognize which deviations are significant enough to trigger further review. It is essential to prepare operating procedures with well-defined limits for process variables for all common tasks. Once onsite personnel are trained on MOC policy and are knowledgeable about normal limits for process variables, they can make informed judgments regarding when to apply the MOC system.
Once a deviation is identified that triggers the MOC system, it is management’s responsibility to gather the right people and resources to review the situation. The skills of a multidisciplinary team may be required to thoroughly identify potential hazards, develop protective measures, and propose a course of action.
Here are some interesting photos of “fixes” that are clearly not design that I have seen in my time.
In this photo, there are three open block valves. There’s no way to get a fresh sample because it’s not in the process flow.
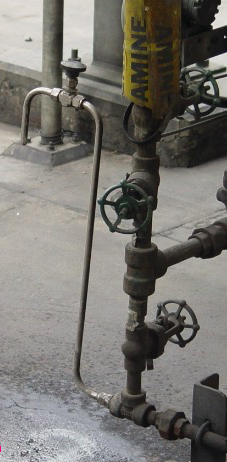
Here’s another good one. That red object is an actual broom handle jammed into the button to prevent shut-off to the winch.
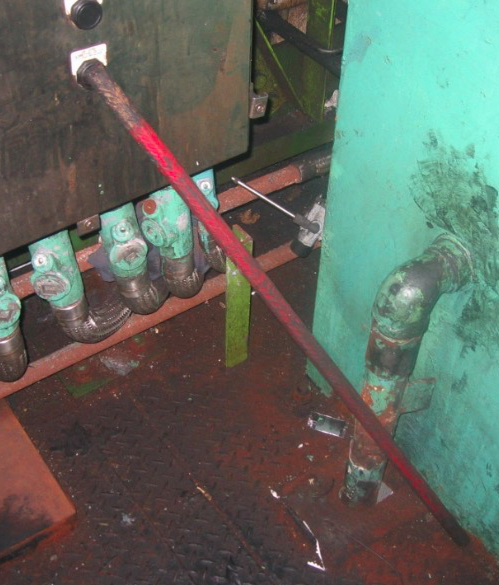
In this photo, you can see a highly caustic substance pooling on the ground. Notice the glass bottle set-up for catching the substance.
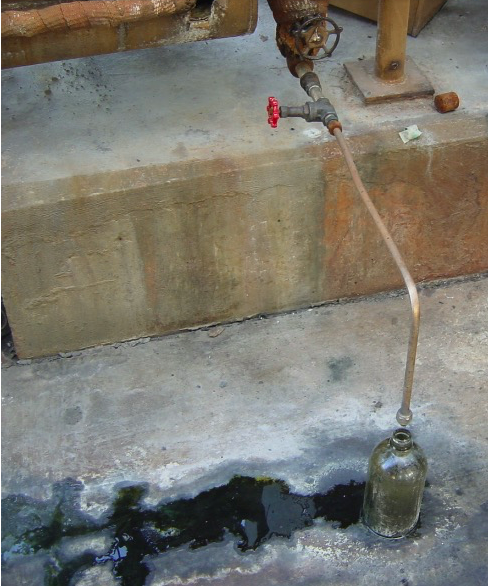
This one needs no explanation:
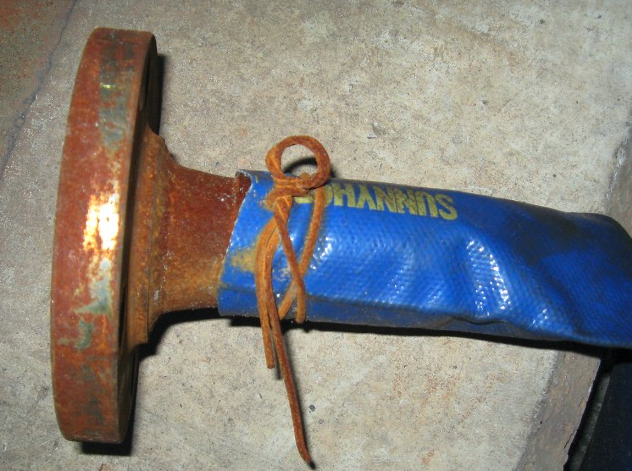
Here are two images of homemade sample stations, designed to cool the product down. But what if the substance isn’t cool enough? And how do you get a fresh sample?
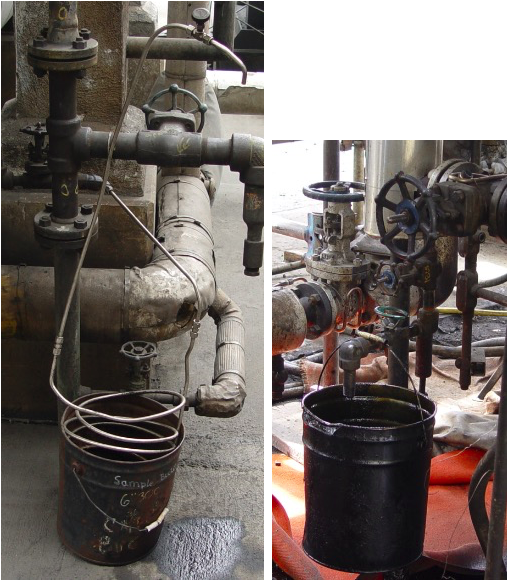
Explosions and injuries happen all the time from “fixes” like these and it breaks my heart to see the guys on the ground subjecting themselves to these unnecessary dangers. As operators, we should not take it upon ourselves to operate equipment routinely bypassing the SIS, failed equipment, or motor-operated valves, without using Management of Change it is our job to pass the issue up the food chain to upper management. It shouldn’t be our burden to bypass protocols because the issues aren’t being fixed. That’s why MOC exists– to keep the equipment operating and to avoid costly shutdowns and repairs. But more importantly, to keep the workers safe.
Additional resources on Management of Change:
https://www.csb.gov/assets/1/20/moc082801.pdf?13886
http://blog.stpub.com/bid/203455/Chemical-Safety-Board-Recommends-Better-Process-Safety-Management
For more on safety in the coker, visit Gary’s Blog.
Leave a Reply
You must be logged in to post a comment.