FREE
Facilitator: Ryan Schoel – REFCOMM®
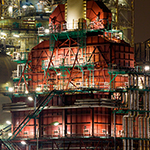
The heater charge pump is arguably the most critical pump in the entire delayed coker. It can also be the most challenging to keep properly ready in standby mode so it is hot and ready when called into action and QUICKLY…..During this session, we will be discussing best practices regarding standby operation, returning the pump from maintenance to a standby ready state, and special considerations for cold climates. There are additional strategies to consider if you have an auto-start system and/or a variable frequency drive (VFD) type system.
Webinar Recap
The eRefcomm® series rolls on, this time with a more operations focused topic, “Making Sure your Spare Heater Charge Pump is Ready for Action” with the presenter Ryan Schoel from the Coking.com team. The discussion was active in all the platforms, Zoom, Slido, and chat. Thank you for everyone that contributed to the discussion! The following is a summary of the event, but much more information was shared than is presented here. It is a reminder to everyone who stumbles across this page – the eRefComm® events are not recorded and not available after the fact. You need to be there to get the wisdom and experience of the group and the SMEs.
The heater charge pump is the literal heart of the unit. Mean Time Between Repair (MTBR) for most refinery pumps can exceed 48-60+ months for best-in-class refiners in many services. From our kick-off poll question, it was insightful that, with this particular pump, most of the respondents were only achieving a run time of 6-18 months. There were some outliers with 36+ months, but that was only two of the plants represented. It is clear, we as an industry, have our work cut out to improve the reliability of these pumps.
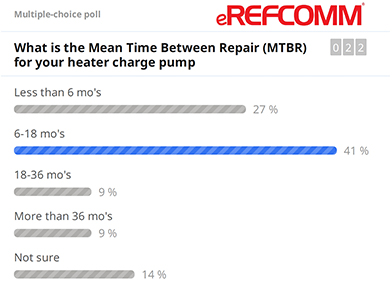
Getting the pumps ready and in hot standby is a critical activity to ensure the long-term health of that spare pump to start in an unexpected basis. Given the short MTBR, it is probable the spare pump will be called upon in a sudden way…typically on a Sunday night or on a holiday.
So how do we get the pump ready?
Many topics were discussed around the bearings, seal flushes, lube oil or lubrimist systems, and drivers. However, the focus was on the warm-up and how to ensure the pump is hot! It was notable that most of the respondents to the next poll had insulated their pumps, but some had not. In our global consulting travels, we have seen a number of plants where the pump insulation was missing or in disrepair. It seems obvious but starting with “the basics” promotes a good foundation for subsequent actions.
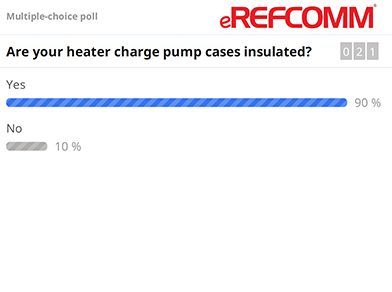
A review of various warm-up line configurations was shown. Over time, systems have evolved from a simple short bypass around the discharge check valve to more elaborate schemes with multiple flow paths to all the operators to adjust the flows, especially to the lower sections of the case. The general thinking is that by bringing the warm-up material lower into the case will result in a better chance for ensuring uniform heating. However, the size of lines, length, minimum flow positions (if applicable), and case geometry make it impossible to provide a one-size-fits-all approach. The best practice is to use IR guns and even better, IR cameras to develop a procedure that works for your plant.
The control of the warm-up flow was a subject of discussion. Again, these systems have evolved due to erosion from coke fines and high pressure drop. Designs such as wide body globe valves or notched or drilled gate valves (single or multiple in series) have shown improved life over “standard” valves. Knowing how many threads to open the valve in its new state and eroded or plugged state is more of an art than a science and requires good attention to details by the operators and reliability teams
There was a short but useful discussion during the Q&A about bringing these pumps back into hot standby after maintenance, when these pumps are filled with light flush material and have to be slowly lined up so as to not trip the running pump due to light oil flashing and cavitation. There is also the aspect of hot alignment that is necessary after putting the pump back in the hole. The recommended guideline is a heat-up rate of less than 100°F/hour and then hot alignment within 50°F of the online pump temperature if possible.
Relying on a spare pump auto-start is a subject of debate in the industry. Some people love them, and others don’t trust them. The poll indicated that only a slight majority did not have an auto-start system. The sites which had auto-start systems, the testing frequency varied significantly. Our recommendation is for you to treat the auto-start testing like you would a PSV. If it works successfully, you can extend the testing interval. If it fails to start on demand, then you should test more frequently. It’s simple but not many plants do this, in our experience. Remember, when testing this pump or swapping the pumps, it is important to have a team of operators stationed at critical locations around the unit to deal with any upset quickly.
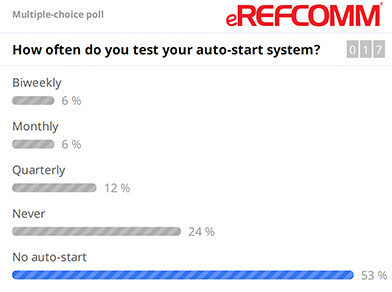
Question, how do you manage the heater trip interlocks during this time?
In summary, this pump can be reliable and run for a long time with the right attention to details. If your pump is not achieving a MTBR of >24 months, adopting some of these ideas might help. If you would like more details or ideas, please reach out to us at info@coking.com for additional support.
Again, a big Coking.com thanks to all of you who participated and shared your wisdom and experience. We are all smarter together as one refining community.