What I like to point out in my audits is what makes the most sense for the good of the unit. I have completed a lot of unit audits worldwide and I see a common thread between them all, and that is the need to check and recheck all of the equipment every shift– always. When you think about it, the surveillance round should be the operator’s primary mission. But often the operators don’t have much of a say in how the surveillance rounds are conducted or in what should be checked and when.
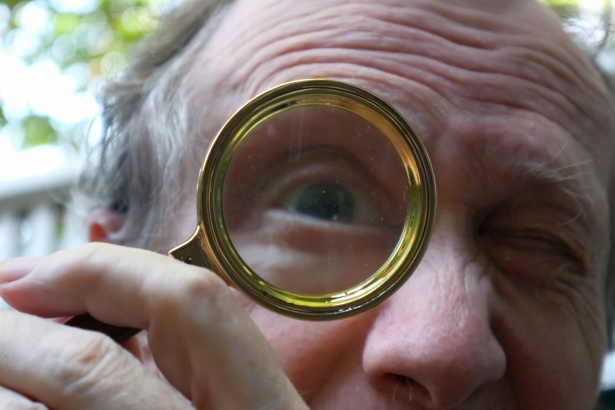
Refinery surveillance rounds are important for preventing accidents, injuries, & equipment failures
There are millions of dollars worth of equipment out there running in the unit. There is some monitoring on it, but not very much. Operators are the eyes, ears, nose, and feel of the equipment. But I feel we have gotten away from this basic need. Our jobs have gotten more administrative as time has gone on, but really the operators are there to monitor the hundreds of pumps, fans and instrumentation that are running continuously, as well as all the other things that could go wrong in the unit, including line shifts, leaks, and vapor clouds.
Operators need to be aware of the most efficient way to walk through the unit to look at the most primary equipment in a routine fashion. And while at certain pieces of equipment, operators need to check in with the control board. I believe there isn’t as much communication as there used to be. A lot of folks have gotten away from engaging in routine conversation–from the people outside to the people inside the control room.
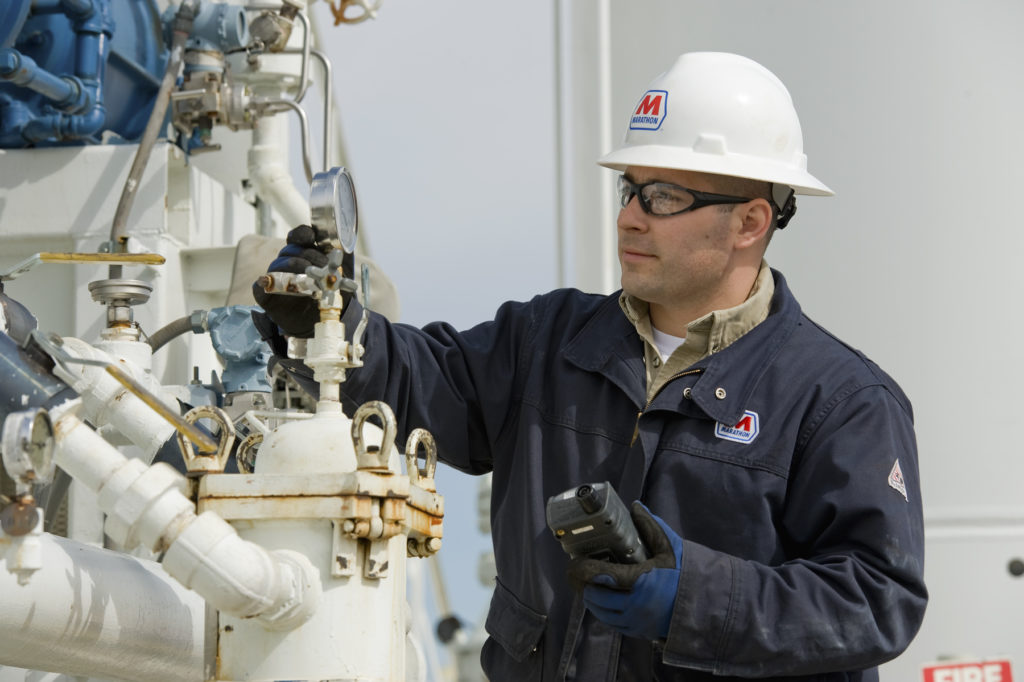
Photo credit Marathon Oil. Refinery engineer inspecting equipment, valves, and gauges to prevent shutdowns
When I talk about outside verification, I mean that these control valves have position indicators on them. Let’s say control valve FC126 is 35% open and allowing 130 barrels of flow. But sometimes what happens in the unit is that valve may not be showing the same as what the control board is seeing; upstream and downstream there are temperatures, pressures and levels that can be affected by a flow control valve. It’s important to verify the outside process to what the control board is seeing (sometimes) a mile away.
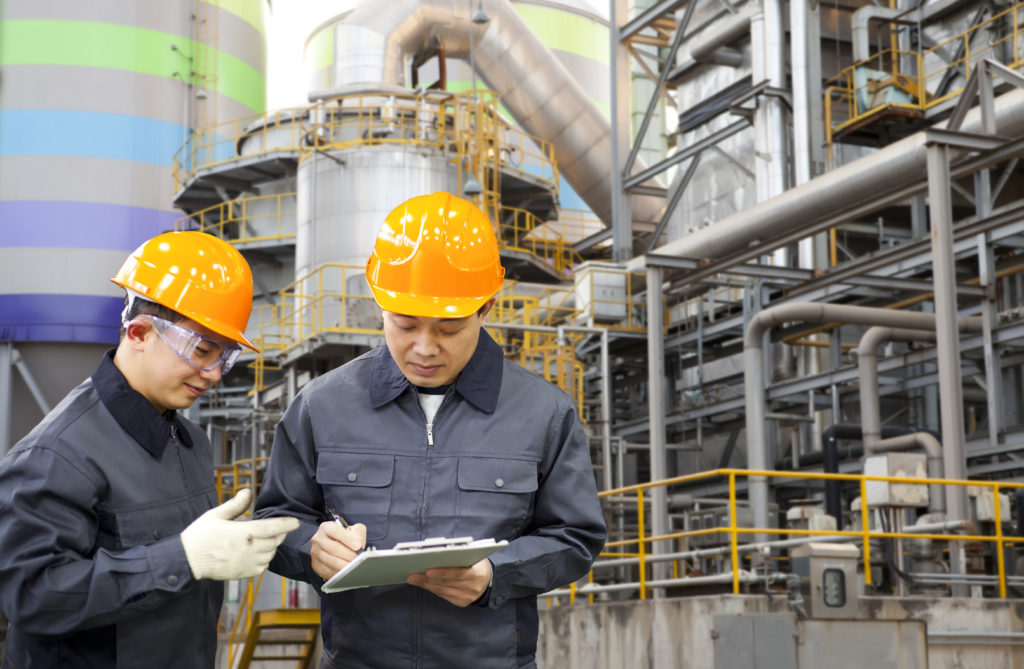
Refinery operators should implement an inspection system for the unit to prevent accidents, injuries, and equipment failures.
Are we willing to bet our lives on a wire the size of a pencil lead? The pressure gauge outside should be showing the same pressure from the PT that they see at the board. Our job on surveillance rounds is to verify that what the board is seeing is real and what we are seeing correlates to what he/she sees.
And too many times we are not doing that. Some examples of routine things to check: pump suction pressure, pump discharge pressure, heater flow indication and local temperature indicators; each heater coil valve position. … I could list 200 items that we should be checking. It’s about knowing the unit intimately so that you know when something is wrong. That’s one of the primary objectives of being a unit operator.
To put this in perspective, I will share a little story. A few years back, I was doing an audit with an operator who had eight years experience in the unit. We’re up on the fin fan deck. Now, I was always taught to inspect each fan, to look and listen for vibrations. There are 30 fans in this unit. One of the fin fans is squealing. The motor is turning at its usual RPM but the belt is too loose and the motor is screaming like crazy. The operator I am with just walks right by it.
“What about that? Don’t you guys usually shut them down when they’re in this condition?” I ask him.
“Not without the board telling us to,” he responds.
“Does the board know the belt is lose?”
“I don’t know,” was his response.
He refused to do a single thing about it. For me, it was shocking that the equipment was malfunctioning at that level and there was no sense of urgency surrounding it. I don’t know what ended up happening with the fan but I will bet a month’s salary that the motor finally overheated and caused the fan to be out of service, which probably resulted in an expensive repair and an even more expensive shutdown.
The key takeaway for this story is that operators can and should feel empowered to manage surveillance rounds in their house.
_______________
For more coking and safety content, visit Gary’s Blog.
Connect with Gary on LinkedIn.
Leave a Reply
You must be logged in to post a comment.