— By Justine Arnold, Coker Process Engineer at Chevron
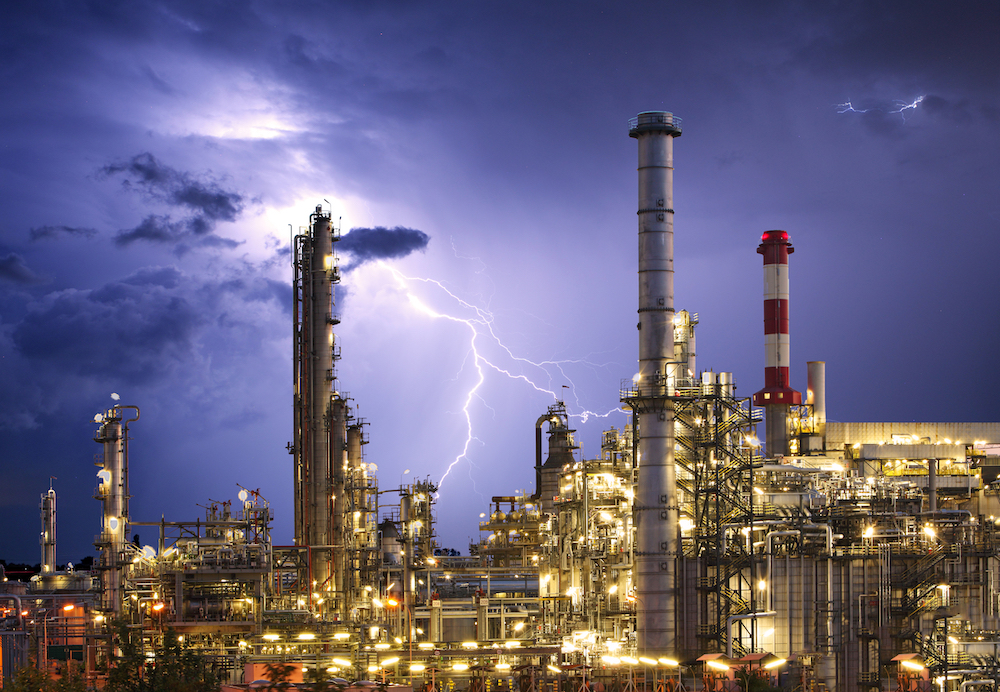
Did you know that in your lifetime, you have a one in 3,000 chance of getting struck by lightning? In any one given year, the odds of becoming a lightning strike victim in the U.S. alone are one in 700,000. According to the National Geographic, “Earth as a whole is struck by an average of more than a hundred lightning bolts every second.” And with static structures, the odds are even greater. According to the National Lightning Safety Institute, a house or similarly-sized building has a one in 200 chance of being struck by lightning every year.
Given these odds, the chances of your refinery unit being struck by lightning are not as slim as you previously might have thought. In fact, a quick search on Google reveals dozens of stories documenting refinery lightning strikes and refinery fires caused by lightning over the years. Lightning strikes are fire hazards anytime they strike, but the risk of injury and fire is exponentially greater to refinery structures because of the very nature of their work. Lightning strikes on refineries can release toxic fumes, cause injury and death, and create millions of dollars in damages in mere seconds.
El Segundo Lightning Strike
On January 31, 2019, lightning struck a power pole at Chevron’s El Segundo Refinery’s Sulfur Acid Division. This resulted in a power dip at several substations throughout the refinery and a complete power outage at the sulfur units. In addition to temporary power loss to several units within the refinery, all units were required to begin cutting back feed immediately to address the SRU power outage, including the coker.
During the power dip, the coker unit experienced a loss of all electric pumps, (including the feed, overhead accumulator, and HCGO pumparound), as well as a loss of furnace-induced draft fan. The impact of the power outage affected all three coke modules. Each module was at a different point in the drum cycle and needed to be handled differently.
Luckily for Chevron, the Coker Operations team already had a plan in place that clearly outlined recovery priorities in the event of a lightning strike, and the team was able to effectively mitigate three potentially tarry drums without a safety or environmental event.
The recovery plan, outlined in the graphic below, included the following action items:
- Furnace Charge Pumps: Avoid loss of flow case
- Fractionator Overhead System: Keep overhead compressor online to avoid flaring
- Furnace CO’s: Minimize fuel gas to reduce risk of explosive environment
- HGO P/A System: Avoid loss of flow and plugging
- Distillation Product Pumps: Manage column levels
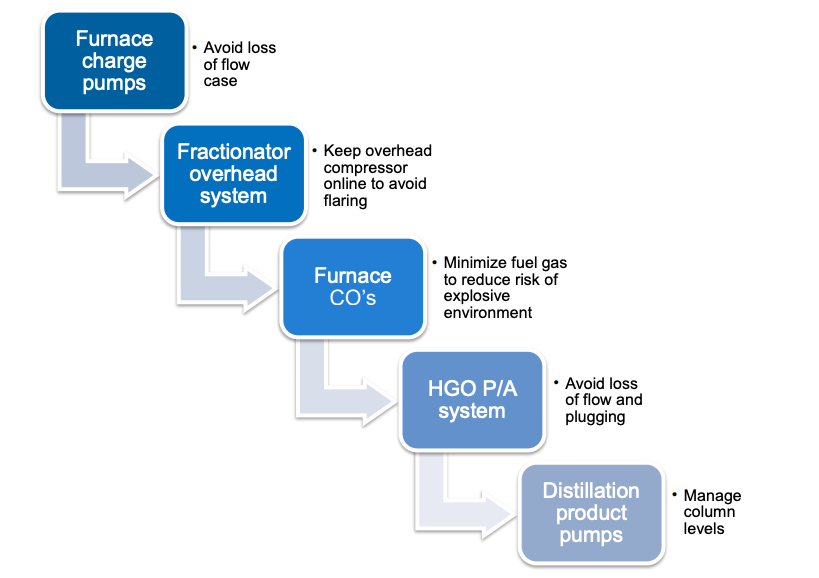
Handling Tarry Drums
The F-501A drum was fed below coking temperatures for 10 minutes before the module was bypassed. The F-501A transfer temperature reached 675 degrees F during the power dip recovery. Included in the recovery plan recommendations was that if feed was available, the team should switch feed to adjacent drum and increase steam strip to 1.5 hours. Because of unit slowdowns elsewhere in the refinery, they had extra time and decided to be conservative with handling the tarry drums, opting to steam strip for 4 hours instead of the proscribed 1.5. The Coker Ops team was proactive and organized in their response to the lightning strike. Similar paths were executed for the B and C drums, with the extra time being allotted to more time for steam stripping.
In addition to managing the partially completed coke drums, the operations team had to troubleshoot some additional issues created by the power outage related upset. Some coke was dislodged from upstream and partially plugged the HCGO stripper level control valve. Similarly, the HCGO product steam generator was believed to be partially fouled as a result of the upset as well.
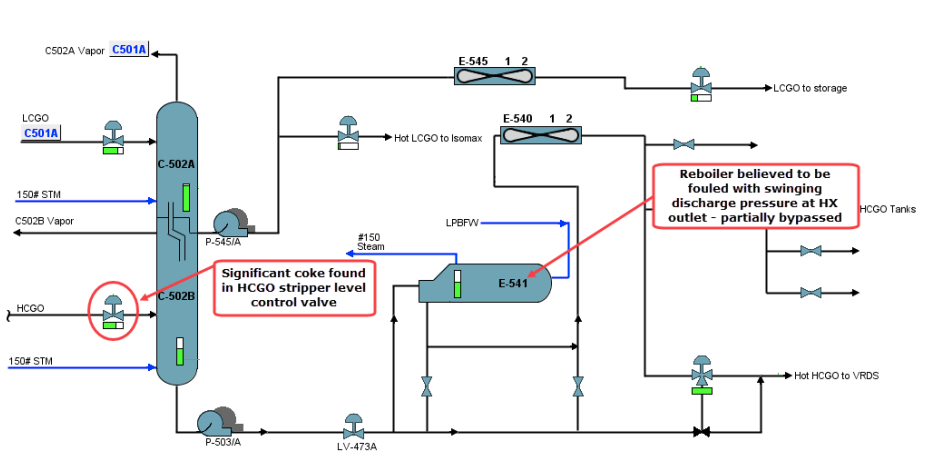
But because of the Coker Ops team’s thorough preparation, organization, and conservative approach, all pumps and fans were safely returned to service. There were no hot spots or blowbacks during the drum cuts. There were no step changes in the furnace skin temperatures or fouling rates following the incident and no foamovers resulting in vapor line dP.
Chevron provided an example below of a flow chart for how to manage the tarry drums. In addition to the flow plan, they also had a plan for how to attack their pumps and get them back on line with some kind of priority. Their actions shows the need to have an actionable plan and an ability to execute said plan, but even more importantly, their plan demonstrated the need to have some flexibility in your plan and to err on the conservative side when time allows.
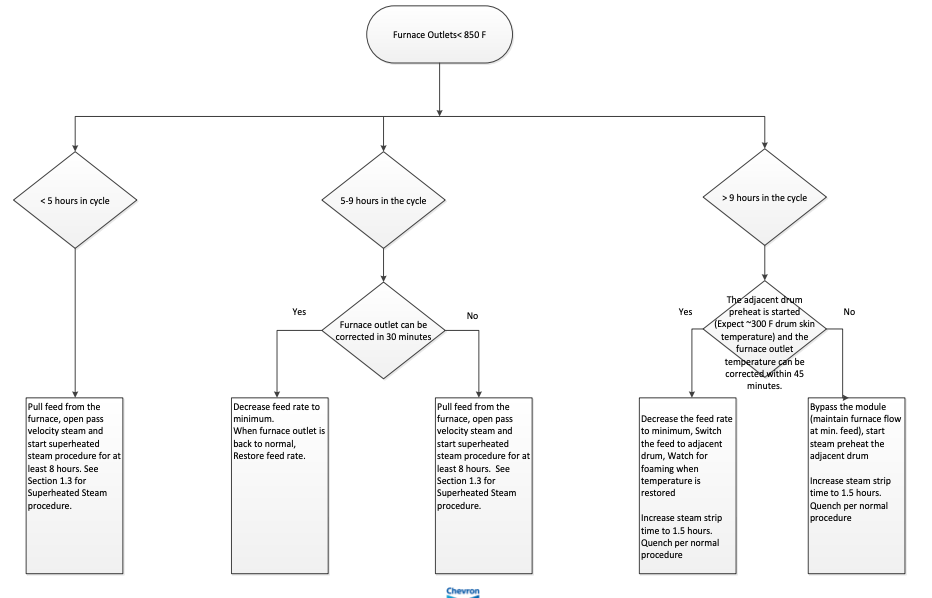
The above article was adapted from a presentation Justine Arnold gave on behalf of Chevron at RefComm® Galveston 2019.
Do You Have a Plan?
Considering the high probability of lightning striking and the damage it can cause to refineries and workers, the million dollar question to ask yourself is this: does your site have a plan in place for managing a lightning strike? Do you have a plan for prioritizing and getting equipment back online, and if so what’s the basis for that plan? The El Secundo site had a plan and a flow chart. And it paid off for them. But surprisingly, we at Coking.com have worked with many of the top refineries around the world and most of them don’t have one. We offer this as part of our consulting services. Let us help mitigate your risk to the best possible outcome in the event of a natural disaster. Visit our consulting page to learn more about our services, or reach out to us at info@coking.com.
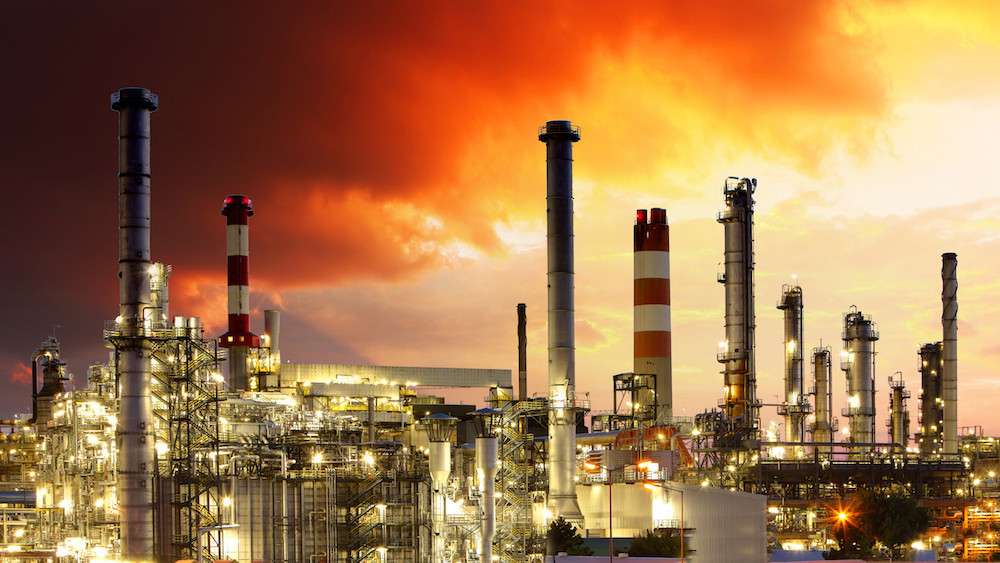
Click here for the Chevron’s full presentation, or visit our Past Presentation page to learn more about refinery safety, technology, and best practices.
The American Petroleum Institute recently released an update to their fire prevention standards and safety protocols. To learn more about it visit: https://www.api.org/news-policy-and-issues/news/2019/07/02/api-updates-fire-prevention-and-safety-recommended-practice-for-refineries
Leave a Reply
You must be logged in to post a comment.